Como equipamiento indispensable en las cocinas modernas y en la pequeña producción industrial, la calidad de las batidoras está directamente relacionada con la experiencia y la seguridad del usuario. Como fabricante profesional de batidoras, somos muy conscientes de la importancia de la calidad del producto. A continuación le mostramos cómo nuestra fábrica garantiza la calidad del producto.
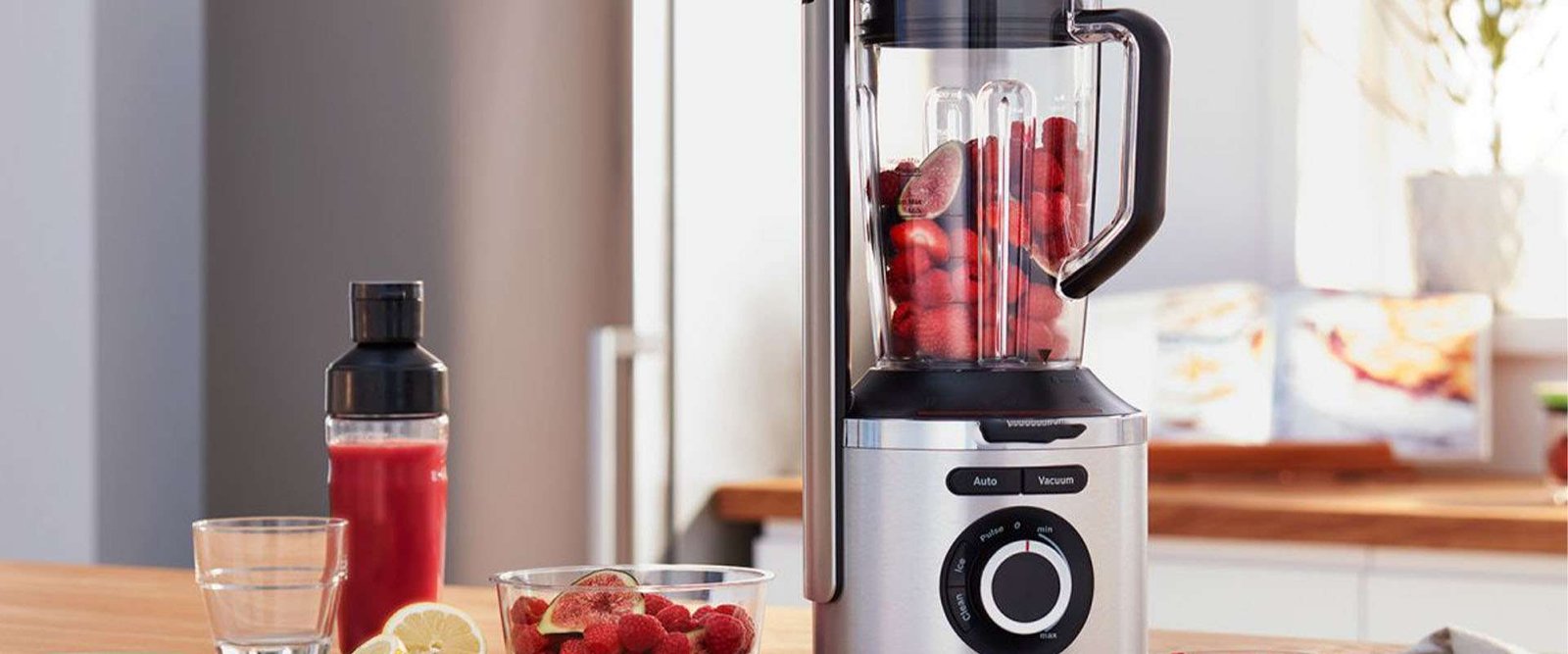
Ⅰ. Control de calidad en la fase de diseño
Estudio de mercado y análisis de la demanda Antes de diseñar la mezcladora, realizaremos un estudio de mercado en profundidad para comprender las necesidades de los usuarios, analizar las tendencias del sector y asegurarnos de que el diseño del producto satisface la demanda del mercado.
Revisión del plan de diseño El diseñador elaborará un plan de diseño basado en los resultados de la investigación y, a continuación, un equipo de expertos lo revisará para garantizar la racionalidad y viabilidad del plan de diseño.
Selección de materias primas La selección de materias primas de alta calidad es el primer paso para garantizar la calidad del producto. Examinaremos estrictamente a los proveedores para asegurarnos de que todas las materias primas cumplen las normas internacionales.
II. Control de calidad en la fase de producción
Producción de prototipos y pruebas Antes de la producción formal, fabricaremos prototipos y realizaremos pruebas rigurosas, incluidas pruebas funcionales, pruebas de durabilidad y pruebas de seguridad, para garantizar que los prototipos cumplen los requisitos de diseño.
Configuración de la línea de producción Nuestras líneas de producción utilizan equipos de producción y tecnología avanzados para garantizar la automatización y estandarización del proceso de producción y reducir los errores humanos.
Supervisión del proceso de producción Durante el proceso de producción, contamos con un equipo dedicado a la supervisión de la calidad que supervisa cada eslabón en tiempo real para garantizar que el proceso de producción cumple las normas de calidad.
Ⅲ. Control de calidad en la fase de inspección
Inspección del material entrante Todas las materias primas que entran en la línea de producción deben ser estrictamente inspeccionadas, y los materiales no cualificados serán devueltos al proveedor.
Inspección en línea Durante el proceso de producción, una persona especializada realizará inspecciones aleatorias de los productos semiacabados y acabados para garantizar la calidad del producto en cada paso.
Inspección del producto acabado Después de que el producto acabado salga de la línea, se llevará a cabo una exhaustiva prueba de rendimiento y una inspección de aspecto para garantizar que cada mezcladora cumple las normas de fábrica.
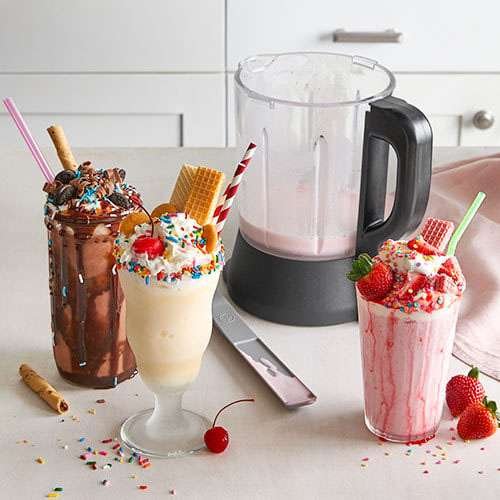
Ⅳ. Medidas de garantía de calidad
Formación del personal Proporcionamos formación periódica sobre habilidades y seguridad al personal de producción para mejorar su concienciación sobre la calidad y sus habilidades operativas.
Mantenimiento del equipo Mantenemos y calibramos regularmente el equipo de producción para garantizar un funcionamiento preciso del equipo y reducir los errores en el proceso de producción.
Sistema de gestión de la calidad Nuestra fábrica sigue el sistema de gestión de la calidad ISO y mejora continuamente la calidad de los productos mediante la mejora continua.
Ⅴ. Servicio posventa y comentarios
Servicio posventa Ofrecemos un servicio posventa completo, que incluye la instalación del producto, orientación sobre su uso, resolución de problemas, etc., para garantizar la satisfacción del usuario.
Opiniones de los usuarios Valoramos las opiniones de los usuarios y optimizamos continuamente el diseño de los productos y los procesos de producción recogiendo y analizando las opiniones de los usuarios.
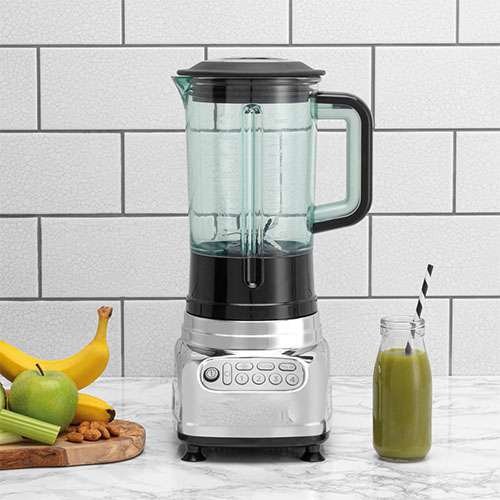
Ⅵ. El cliente primero: ofrecer servicios integrales
Sabemos que la satisfacción del cliente es el motor principal del desarrollo empresarial. Por ello, siempre nos centramos en el cliente y le ofrecemos servicios integrales.
En nuestra fábrica, la calidad del producto es siempre la máxima prioridad.
Desde el diseño hasta la producción, desde la inspección hasta el servicio posventa, hemos establecido un completo sistema de control de calidad para garantizar que cada mezcladora pueda satisfacer las expectativas de los usuarios.
Al revelar nuestro proceso de producción, esperamos que los usuarios confíen más en nuestros productos, porque sabemos que la calidad es la vida de una empresa y nuestro compromiso con los usuarios.